
Extensive review of manufacturing and assembly process data, along with product testing, may be used as a type of validation for devices manufactured individually or on a one time basis. Retrospective process validation may be used, if adequate, for products which may have been on the market without sufficient pre-production process validation. Product qualification for process validation may take place during design validation. Or, certain product specifications may have been changed to make the product easier or less expensive to manufacture, but these changes may adversely affect product performance. In other words, the product produced by the validated process should be checked to determine whether the process has had any adverse effect on the product or its performance.įor example, radiation sterilization may result in degradation of plastic devices which can lead to premature failure. These changes would need to be validated.įinally, the product should be qualified. It is important to remember that validation is dynamic and specifications and parameters may be changed as a result of the validation efforts. The requirement to develop the process can be traced back to 820.70(a).
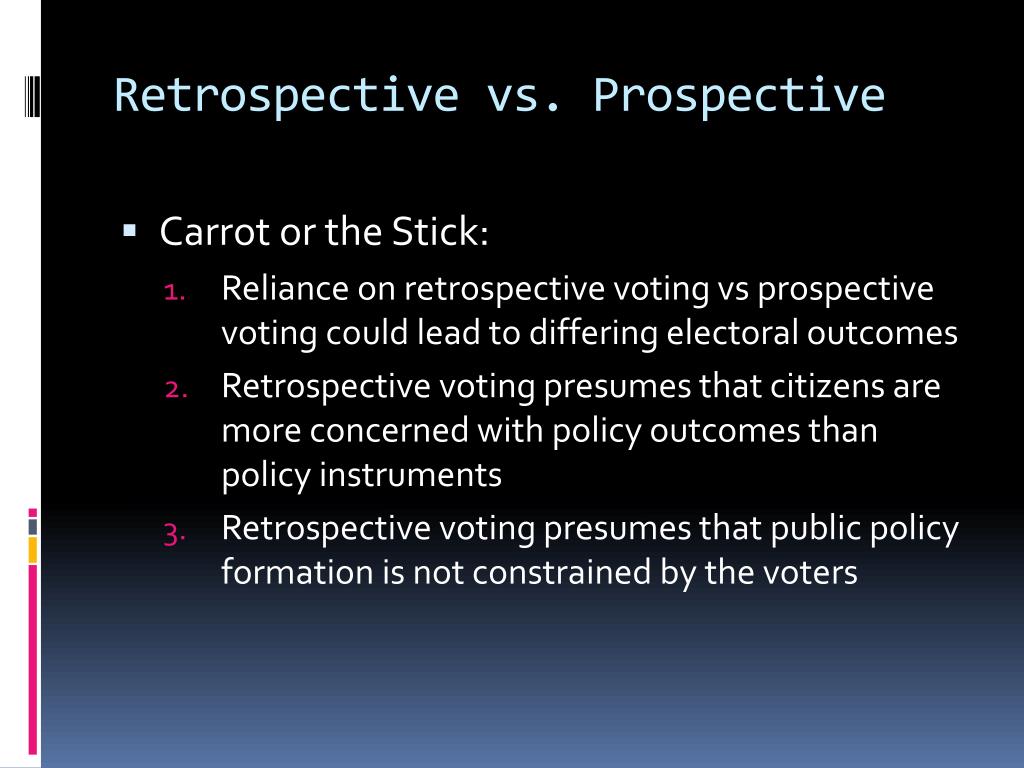
show that it consistently operates within established parameters and produces results or products that meet specifications) until the process is fully developed, and appropriate parameters have been established. It is impossible to validate a process (i.e. From time to time we see manufacturers who try to validate processes before they have completely developed them and established process parameters. The process must be developed before it can be validated. Installation qualification is essential for successful process validation. The requirement for equipment qualification can be traced back to 820.70(g). When equipment is moved, a new installation qualification should be performed. Installation qualification does not have to be performed again if it was recently done for a previous validation. If the equipment is found to be out of calibration at the end of the study, the validity of the results is called into question. Equipment should be calibrated before and after process validation to determine whether the equipment remained in calibration during the entire process validation study. Installation qualification should be conducted for equipment used in a validated process to assure that the equipment has been properly installed, meets the device manufacturer's specifications and requirements for it, and is capable of operating in the range required for the process being validated.ĭuring installation qualification, equipment maintenance and calibration schedules and procedures should be established.

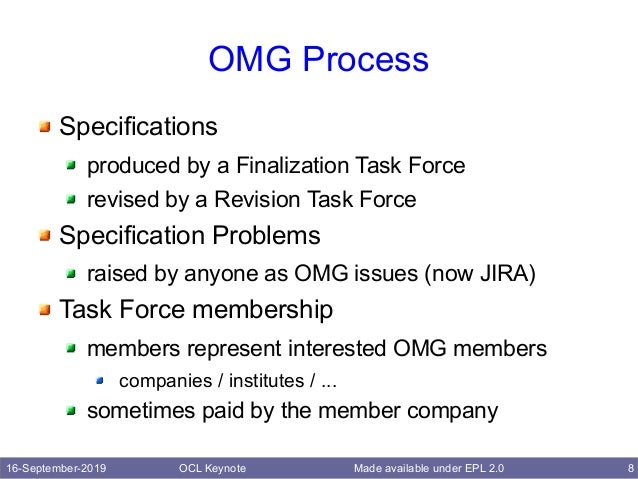
The validation program must be planned and documented, and the validation results must be documented and maintained. Prospective validation includes considerations made before a new product is introduced, or when there is a manufacturing process change which may affect the product's characteristics. Generally, process validation is a pre-production activity. Retrospective process validation is validation of a process for a product already in distribution based upon accumulated production, testing and control data. Prospective process validation is validation conducted prior to the distribution of either a new product, or a product made under a revised manufacturing process, where the revisions may affect the product's characteristics. Process validation means establishing by objective evidence that a process consistently produces a result or product meeting its predetermined specifications. The lack of a subsequent inspection and test should be stated in the EIR along with any process validation issues. Before inspecting a manufacturing process for process validation, it is important to determine if the results of the process cannot be fully verified by subsequent inspection and test. The QS/GMP does not require the validation of all manufacturing processes.
